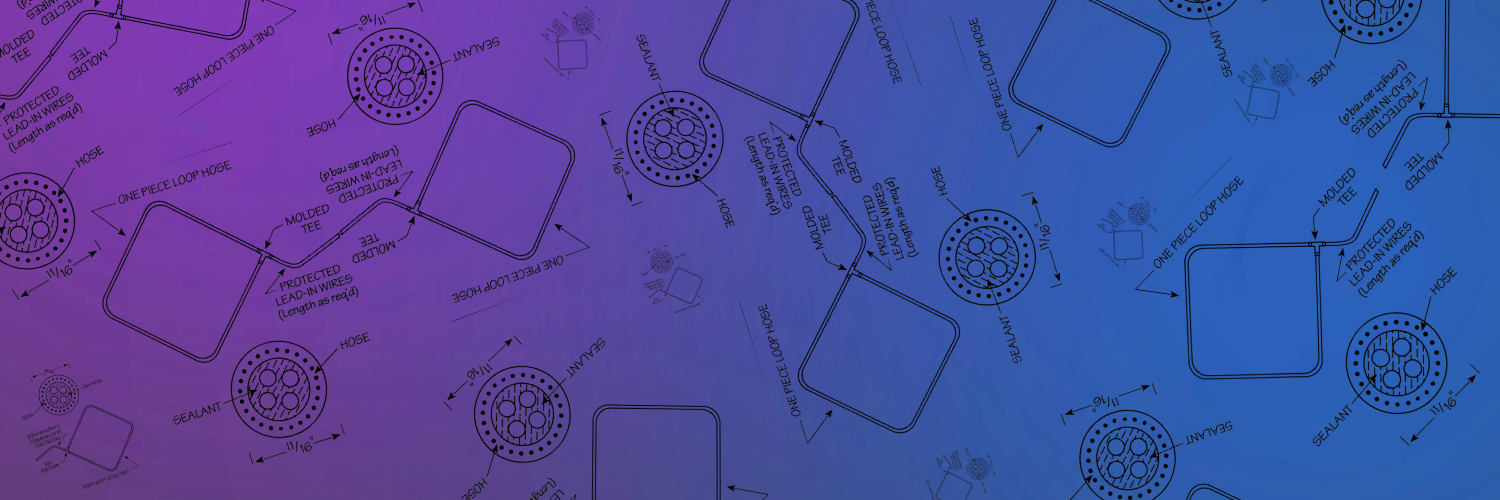
Model H50 Preformed Loop
The Model H50 loop is very durable, and has all the same features as the Model HDR in a more compact design for an easier saw cut installation. This model uses a smaller O.D. hose with #18 TFFN copper (1/2” outside diameter). The loop has no preformed corners so it can conform to any configuration, and will flex with the pavement. These loops can be ordered in square, rectangle, round, double or quadrupole configurations. Each loop is custom built to your specifications. The key features of the Model H50 are:
This heavy duty rubber loop is designed for easy installation in a saw cut.
Ultimate wire protection: loop will last as long as other equipment at intersection.
Excellent moisture protection.
Easy, inexpensive installation when taped down and paved over.
No need to damage new pavement to saw cut in loops.
Shifts and conforms to pavement movement.
Direct burial in gravel.
Minimal joints reduce weak points.
Loop and home run filled with polyurethane. Material cures chemically not hot melt. Material will not soften or harden in extreme weather.
Model H50 Cut Sheet & Specs
-
Loop and homer constructed using 250 psi hydraulic hose. 1/2" outside diameter.
No hose splices except at tee connection.
Tee joint constructed using high temp rubber flexible throughout.
Standard wire is #18 TFFN copper. No splices.
Loop and homerun is filled with polyurethane. Material cures chemically not hot melt. Material will not soften or harden in extreme weather.
Each loop custom built to your specifications (size, turns, and lead lengths).
-
Preformed detector loops shall be factory assembled. Homeruns and interconnects shall be pre-wired and shall be an integral part of the loop assembly. The loop configurations and homerun lengths shall be assembled for the specific application.
All materials used to protect the wire in the preformed loop shall be flexible and shall have properties which will withstand the temperatures and pressure of paving applicators and hot melt sealants without melting or cracking.
-
The loop and homerun shall be constructed using nylon reinforced hydraulic hose, 1⁄2” O.D. Hose for the loop and homerun shall be one piece. No joints or splices shall be allowed in the hose except where necessary to connect the homeruns or interconnects to the loops. This will allow maximum wire protection and loop system strength.
Hose tee connections shall be high temperature synthetic rubber. The tee shall be of proper size to attach directly to the hose to minimize glue joints. The tee shall have the same flexible properties as the hose to insure that the assembly can conform to pavement and shifting without cracking or breaking.
The wire used shall be 18 awg. TFFN copper stranded, standard. The number of turns in the loop shall be application specific. Homerun wire pairs shall be twisted. No wire splices will be allowed in the preformed loop assembly.
The loop and homeruns shall be filled and sealed with a flexible sealant to insure complete moisture blockage. The material shall be two part polyurethane applied at ambient temperature to avoid insulation damage. The material when set up shall not soften in warm temperatures nor get brittle in cold temperatures. This insures proper wire protection at all times.
Loops and wire shall be marked as necessary for the job.
-
Asphalt Overlay: A minimum compacted lift of 2” is necessary to pave loops in. Place the loop in the road, then secure the loop at the corners with straps and nails or asphalt tape. Tape the loop and lead-in every 3-5 feet. We recommend that some asphalt be shoveled over the loop at least on the leading edge to prevent shoving with the paver, as well as wherever the paver tracks will run over the loop. If the whole loop is covered with shoveled asphalt, no taping or strapping is necessary. If paving depth is minimal, cover the entire loop with asphalt tape to avoid reflective cracking. Ideally, the loop should be placed in the gravel subbase and covered with gravel, then paved over. Loops installed in gravel subbase can scratched in to the gravel at any depth. The loops are designed to withstand compaction after installation in the gravel. Loops can also be saw cut in to existing asphalt if overlay depth is insufficient. Loops installed in this manner can be placed in a 3⁄4-1” deep slot, just enough to get the loop below existing surface.
PCCP Concrete: Loops can be secured to the rebar wherever it crosses, using plastic tye-wraps, then simply run the lead-in underneath the rebar into the j-box or hand hole. Loops should be secured at least every 12-18”. We have found that loops installed to a depth of 14-16” in this manner function normally. The loops can also be secured to an existing roadbed using conduit straps or asphalt tape and then concrete can be poured over the loops.
Saw Cut: Mark loop size with a jig, then cut three legs of the loop out. Two of the legs cut shall be where the tee will be placed. Then put the loop in to the slots and pull out to determine the placement of the last saw cut leg. The saw cut needs to be 3⁄4” to accommodate the HDR loop. Chip out the corners to ease the installation of the loop. DO NOT PRY THE LOOP INTO SLOT. Prying the loop may damage the wire inside the loop. We recommend using a hot melt sealant to fill the slot. Do not use a sealant that is too soft, as this will not provide adequate support for the saw cut walls.